CIP : COST IMPROVMENT PROJECT 2 ( ต่อ )
CIP : COST IMPROVMENT PROJECT
จากครั้งที่แล้วเรากล่าวถึง Lean Manufacturing System Lean คือ อะไร? รวมถึงปัญหา วันนี้เราจะมาแก้ปัญหา และวิธีการปรับปรุง ต่อนะครับ
ระบบการผลิตแบบ Lean (Lean Manufacturing System) เป็นระบบการผลิตทีได้รับการยอมรับทั่วโลก โดยคำว่า Lean Production เป็นคำที่กำเนิดการศึกษาเปรียบเทียบระบบการผลิตรถยนต์ระหว่างสหรัฐอเมริกา ยุโรป และญี่ปุ่น โดยเฉพาะประเทศญี่ปุ่นประสบความสำเร็จอย่างสูงในธุรกิจนี้ รวมทั้งมี Productivity ที่ดี
Lean Production นี้มีจุดกำเนิดมาจากระบบการผลิตแบบโตโยต้า (Toyota Production System: TPS)
<b>โดยแนวคิดเรื่อง Lean นั้นมีองค์ประกอบสำคัญอยู่ 5 ประการคือ
การกำหนดคุณค่าของสินค้า หรือบริการ
การแสดงสายธารแห่งคุณค่าหรือผังแห่งคุณค่า
การทำให้คุณค่าเกิดการไหลอย่างต่อเนื่อง
การให้ลูกค้าเป็นผู้ดึงคุณค่าจากกระบวนการ
การสร้างคุณค่า และกำจัดความสูญเปล่าอย่างต่อเนื่อง
โดยสรุปแล้วระบบการผลิตแบบลีน ก็คือ การมุ่งเน้นที่คุณค่า (Value) ของสินค้าหรือบริการ มุ่งเน้นการลดความสูญเปล่า (Waste) ซึ่งแนวคิดนี้จะทำให้องค์กรสามารถทำให้คุณค่าของสินค้า หรือบริการที่ตนเองเป็นผู้ผลิตมีค่าสูงขึ้น หรือมีเสถียรภาพเพิ่มขึ้น โดยที่มีความสูญเปล่าในกระบวนการผลิตลดลง ซึ่งสุดท้ายก็จะส่งผลทำให้ Productivity ของระบบการผลิตสูงขึ้น ซึ่งจะส่งผลต่อการทำกำไรขององค์กรในที่สุด
ดังนั้น การปรับปรุงผลิตภาพด้วยแนวคิด Lean จึงเป็นสิ่งที่มุ่งให้ความเข้าใจแนวคิด Lean และหลักการของระบบการผลิตแบบ Lean เพื่อให้ผู้ศึกษานำเอาหลักการไปประยุกต์ใช้ในองค์กร เพื่อเพิ่มผลิตภาพให้กับระบบการผลิตได้
โดยหลักใหญ่ใจความแล้ว ผู้ประกอบการ และผู้บริหาร ต้องการให้การจัดทำระบบ Lean ขึ้นมาก็เพื่อวัตถุประสงค์ ต้องการลดปัญหา และแก้ไขปรับปรุงดังนี้ละครับท่านผู้อ่าน
นำแนวคิดลีน ไปดำเนินการ ทำให้ได้จริงจากแนวทางการแก้ไขการปรับปรุงผลิตภาพในระบบการผลิตความสูญเปล่า (Waste) ความสูญเสีย (Lost) และสร้างคุณค่าให้กับลูกค้า
องค์ประกอบใน Model และเทคนิคที่เกี่ยวข้อง
· การผลิตแบบทันเวลา : Just-In-Time- Material Control ( Pull System / Kanban )
- Level Production - Flexible Operation - Quick Changeover - Continuous-One Piece Flow - Small Lot / Batch Production - Cellular Layout
การสร้างการประกันคุณภาพให้เกิดขึ้นภายในกระบวนการ : Built in Quality
- Manual: Automation Line Stop - Andon System - Error Proofing - Visual Management
· เสถียรภาพการผลิต : Operational Stability
- Total Productive Maintenance - Labor-Machine Efficiency - Supplier Involvement
· การจัดทำมาตรฐานและการปรับปรุงอย่างต่อเนื่อง : Standardization & Continual Improvement
รวมถึงเครื่องมือการจัดการผลิต
ขอต่อจากคราวที่แล้ว เหตุของปัญหา ครั้งนี้เราจะมาปรับปรุงกันจากระบบการผลิตแบบลีน ที่พบในกระบวนการผลิต อันดับต้นๆ
ความสูญเปล่า 7 ประการ (7 Waste or MUDA)
Waste : anything that takes time, resources or space but does not add the valueof the product or service delivered to the customer.
(ทุกสิ่งที่ใช้เวลาในการทำ ใช้ทรัพยากรหรือพื้นที่ แต่ไม่ ได้ทำให้ตัวสินค้ามีคุณค่ามากขึ้น หรือแม้กระทั่งไม่ได้ ทำให้ลูกค้าเกิดความพึงพอใจในการบริการ หรือขนส่ง สิ่งเหล่านั้น เราเรียกว่า ความสูญเปล่า หรือ Waste)font>
ความสูญเปล่า (Waste/Muda) คือ การกระทำใดๆ ก็ตามที่ใช้ทรัพยากรไป ไม่ว่าจะเป็นแรงงาน วัตถุดิบ เวลา เงิน หรืออื่นๆ แต่ไม่ทำให้สินค้าหรือบริการเกิด คุณค่าหรือการเปลี่ยนแปลง
1. การผลิตมากเกินความจำเป็น (Over Production)
การผลิตมากเกินความจำเป็น ก่อให้เกิดปัญหา
1. เสียวัตถุดิบ การทำงานของเครื่องจักร แรงงานคน 2. เสียเวลาขนย้าย, ย้ายไปแล้วก็ย้ายมา 3. เปลืองพื้นที่จัดเก็บ 4. ขาดความปลอดภัย ของมากอาจกีดขวางและดูแลลำบากอาจพลัดล้ม 5. เปลืองเวลาการผลิต 6. ของเสียไม่ได้รับการแก้ไขทันที
การปรับปรุง
1. บำรุงรักษาเครื่องจักรให้มีสภาพพร้อมผลิตตลอดเวลา
2. ลดเวลาการตั้งเครื่องจักร โดยศึกษาเวลาในการตั้งเครื่องจักร จากนั้นทำการปรับปรุง
- จัดเตรียมเครื่องมือและอุปกรณ์ให้พร้อมก่อนเริ่มตั้งเครื่อง - แยกขั้นตอนที่ทำได้ในขณะที่เครื่องจักรยังทำงานอยู่ออกจาก ขั้นตอนที่ต้องทำเมื่อเครื่องจักรหยุดเท่านั้น - จัดลำดับขั้นตอนในการตั้งเครื่องจักรให้เหมาะสม - กระจายงานอย่างเหมาะสมโดยไม่ให้เกิดการรองาน - จัดหา/ทำอุปกรณ์เพื่อช่วยในการกำหนดตำแหน่งอย่างรวดเร็ว 3. ปรับปรุงขั้นตอนที่เป็นคอขวด (Bottle-neck) ในกระบวนการเพื่อลดรอบเวลาการผลิต
4. ผลิตในปริมาณและเวลาที่ต้องการเท่านั้น
5. ฝึกให้พนักงานมีทักษะหลายอย่าง
2. การมีสินค้าคงคลังมากเกินความจำเป็น (Excess Inventory)
สินค้าคงคลัง ประกอบด้วย
การมีวัตถุดิบ (RM) งานระหว่างกระบวนการผลิต (WIP) สินค้าสำเร็จรูป (FG) วัสดุสิ้นเปลือง อะไหล่ การมีสินค้าคงคลังมากเกินความจำเป็น ทำให้การไหลของ ผลิตภัณฑ์ (Flow) ไม่ดีเท่าที่ควร
ปัญหาจากการมีสินค้าคงคลังมากเกินความจำเป็น
1. ใช้พื้นที่จัดเก็บมาก 2. ต้นทุนจม 3. วัสดุเสื่อมคุณภาพ (หากระบบการควบคุมวัสดุคงคลังไม่ดีพอ) 4. สั่งซื้อซ้ำซ้อน (หากระบบการควบคุมวัสดุคงคลังไม่เพียงพอ) 5. ต้องการแรงงานและการจัดการมาก
การปรับปรุง
1. กำหนดระดับในการจัดเก็บ มีจุดสั่งซื้อที่ชัดเจน
2. ควบคุมปริมาณวัสดุโดยใช้เทคนิคการควบคุมด้วยการมองเห็น (Visual control) เพื่อให้สามารถเข้าใจและสังเกตได้ง่าย
3. ใช้ระบบเข้าก่อน-ออกก่อน (First in first out) เพื่อป้องกันไม่ให้มีวัสดุตกค้างเป็นเวลานาน
4. วิเคราะห์หาวัสดุทดแทน (Value engineering) ที่ สามารถสั่งซื้อได้ง่ายมาใช้แทน เพื่อลดปริมาณวัสดุที่ต้องทำการจัดเก็บ
3. การมีของเสีย (Defects)
ปัญหาจากการมีของเสีย
1. ต้นทุนวัตถุดิบ เครื่องจักร แรงงาน สูญเสียไปโดย เปล่าประโยชน์ 2. สิ้นเปลืองสถานที่และค่าใช้จ่ายในการจัดเก็บและกำจัดของเสีย 3. เกิดการทำงานซ้ำเพื่อแก้ไขงาน 4. เกิดต้นทุนค่าเสียโอกาส
การปรับปรุง
1. มีมาตรฐานของงานและมาตรฐานของวัตถุดิบที่ถูกต้อง
2. พนักงานต้องปฏิบัติงานให้ถูกต้องตามมาตรฐานตั้งแต่แรก
3. พยายามปรับปรุงอุปกรณ์ที่สามารถป้องกันการทำงานที่ผิดพลาด (Poka-Yoke)
4. ฝึกให้พนักงานมีจิตสำนึกทางด้านคุณภาพ
5. ให้มีการตอบสนองข้อมูลทางด้านคุณภาพอย่างรวดเร็วในทุกขั้นตอนการผลิต (Quick response system)
4. การมีกระบวนการที่ไม่จำเป็น (Unnecessary Processing)
ปัญหาจากการมีกระบวนการที่ไม่จำเป็น
1. เกิดต้นทุนที่ไม่จำเป็นของการทำงาน 2. สูญเสียพื้นที่การทำงานสำหรับกระบวนการนั้นๆ 3. ใช้เครื่องจักร แรงงาน และทรัพยากร โดยไม่ก่อให้เกิดมูลค่าเพิ่มแก่ผลิตภัณฑ์
การปรับปรุง
1. วิเคราะห์กระบวนการผลิตโดยใช้ Operation process chart
2. ใช้หลักการ 5 W 1 H เพื่อวิเคราะห์ความจำเป็นของแต่ละกระบวนการ
3. หากระบวนการทดแทนที่ก่อให้เกิดผลลัพธ์ของงานอย่างเดียวกัน
5. การรอคอย (Waiting)
ปัญหาจากการรอคอย
1.ต้นทุนที่สูญเปล่าของแรงงาน เครื่องจักร และค่าโสหุ้ย ที่ไม่ก่อให้เกิดมูลค่าเพิ่ม 2. เกิดต้นทุนค่าเสียโอกาส 3. เกิดปัญหาเรื่องขวัญและกำลังใจ
การปรับปรุง
1. ศึกษาการเคลื่อนไหว (Motion study)เพื่อปรับปรุงวิธีการทำงานให้เกิดการเคลื่อนไหวน้อยที่สุดและเหมาะสมที่สุดตามหลักการยศาสตร์ (Ergonomics) เท่าที่จะทำได้
2. จัดสภาพการทำงาน (Working condition) ให้เหมาะสม
3. ปรับปรุงเครื่องมือและอุปกรณ์ในการทำงานให้เหมาะสมกับสภาพร่างกายของผู้ปฏิบัติงาน
4. ทำอุปกรณ์ช่วยในการจับยึดชิ้นงาน (Jig, Fixtures) เพื่อให้สามารถทำงานได้อย่างสะดวกรวดเร็วมากยิ่งขึ้น
6. การเคลื่อนไหวร่างกายที่ไม่จำเป็น (Unnecessary Motion)
ปัญหาจากการเคลื่อนไหวร่างกายที่ไม่จำเป็น
การเคลื่อนไหวร่างกายมากเกินความจำเป็น ทำให้สูญเสียเวลาในการผลิตและเกิดความเมื่อยล้า
การปรับปรุง
1. ศึกษาการเคลื่อนไหว (Motion study)เพื่อปรับปรุงวิธีการทำงานให้เกิดการเคลื่อนไหวน้อยที่สุดและเหมาะสมที่สุดตามหลักการยศาสตร์ (Ergonomics) เท่าที่จะทำได้
2. จัดสภาพการทำงาน (Working condition) ให้เหมาะสม
3. ปรับปรุงเครื่องมือและอุปกรณ์ในการทำงานให้เหมาะสมกับสภาพร่างกายของผู้ปฏิบัติงาน
4. ทำอุปกรณ์ช่วยในการจับยึดชิ้นงาน (Jig, Fixtures) เพื่อให้สามารถทำ งานได้อย่างสะดวกรวดเร็วมากยิ่งขึ้น
7. การขนย้ายที่ไม่จำเป็น (Unnecessary Transportation)
การขนส่ง ขนย้ายที่มากเกินไปหรือมีระยะทางที่ยาวไกล ส่งผลกระทบต่อต้นทุนและเวลาในการผลิต
ปัญหาจากการขนย้ายที่ไม่จำเป็น
1. ต้นทุนในการขนส่ง ได้แก่ เชื้อเพลิง แรงงาน 2. เสียเวลาในการผลิต 3. วัสดุเสียหายหากวิธีการขนส่งไม่เหมาะสม 4. เกิดอุบัติเหตุหากขาดความระมัดระวังในการขนส่ง
การปรับปรุง
ควรจัดสถานที่รองรับงานการขนย้ายจุดที่เกิดประโยน์สูงสุด หรือจัดให้มีการขนย้ายลดจำนวนครั้งซึ่ก็มาจากการวางแผนการผลิต และการจัดเก็บ ตามความต้องการของลูกค้า
ครับ นี่ก็เป็นการปรับปรุง ซึ่งสามารถดำเนินการได้เลย นั่นก็ขึ้นอยู่กับองค์กร การจะดำเนินการปรับปรุงแก้ไข ก็ขึ้นอยู่กับปัจจัย องค์ประกอบ เรื่องของคนที่ไม่ชอบเกิดการเปลี่ยนแปลง หรือการเปลี่ยนแปลงก็ต้องใช้เงินทุน
ดังนั้นผู้บริหาร ก็ต้องสนใจหลักการบริหาร เพื่อจูงใจ เทคนิคการบริหารจากคน ส่วนเรื่องเงินก็ต้องวิเคราะห์การลงทุน ลงทุนไปแล้วพัฒนาแล้วทำให้มี การลดต้นทุน ในอนาคตลง เพิ่มประสิทธิภาพงาน และเพิ่มกำไรให้กับองค์กรได้อย่างไร
จะได้นำเสนอโครงการอบรมในหัวข้อต่าง ๆ เพื่อให้ผู้อ่าน ที่สนใจว่าเราควร อบรมหรือพัฒนาตนเองจากเรื่องใดบ้างมาให้อ่านกันเพื่อนำไปพัฒนา ตัวเองเป็นอันแรก จากนั้นถ้านำไปใช้ได้ ตามที่เข้าใจ ย้ำนะว่า เอาไปใช้ได้จริงก็จะเกิดกับทีมงาน และองค์กร
"เพราะปัญหาที่ผ่านมา คนที่ไปอบรม แล้วไม่ได้นำมาใช้ หรือผู้บริหารไม่สนับสนุน และอาจก็เป็นไปได้ ที่ผู้บริหารเองก็ไม่เข้าใจ ทำให้องค์กรพัฒนาได้ช้า และเสียโอกาสต่อการแข่งขัน"
เช่นงาน Lean Manufacturing System ของโครงการ CIP. จะทำได้จริงก็ต้องศึกษาอย่างถ่องแท้ครับ
Download Mind Map Lean vs JIT
//u3.upload.sanook.com/A0/61c1eff323d1f7a72dc1a929bde78ab8
สรุป Lean Manufacturing System
ลีน ( Lean ) เครื่องมือมุ่งสู่การสร้างความได้เปรียบในการแข่งขัน
ในสถานการณ์ปัจจุบัน ซึ่งมีการแข่งขันทางด้านการค้าสูงมากและในแต่ละองค์กรจะมีการปรับกลยุทธ์ในการบริหารองค์กรเพื่อเพิ่มประสิทธิภาพการทำงานโดยคงความกระชันฉับไวไว้ นั่นคือการใช้กลยุทธ์แบบลีน มีแนวคิดพื้นฐานว่า การมุ่งสู่การลดเพื่อความสูญเปล่า หรือ กิจกรรมไร้มูลค่าเพิ่มทั้งหลายภายในองค์กร และต้องดำเนินอย่างต่อเนื่อง
การใช้ลีนมีวัตถุประสงค์อยู่ 2 ประการคือ
คือต้องการประสิทธิภาพมากขึ้น และ ต้องการให้องค์กรสามารถดูแลตนเองได้
หลักของลีนที่ใช้ ในการบรรลุเป้าหมายเพื่อการจัดส่ง คุณภาพ และต้นทุนที่ฉับไว ประกอบด้วย 5 หลักการ คือ 1. คุณค่า เป็นพื้นฐานของการผลิตลีนหมายถึงกิจกรรมใดที่ลูกค้ายินดีที่จะจ่ายเงินเพื่อแลกเปลี่ยนกัน
2. ท่อส่งคุณค่า เป็นแผนผังที่รวมเอากิจกรรมที่มีคุณค่าออกจากการออกแบบใหม่
3. การไหล เป็นการขจัดจุดที่ทำให้หยุดชะงัก ไม่ถูกขัดจังหวะ
4. การดึง เป็นความสามารถในการที่ผลิตภัณฑ์ และกระบวนการสามารถถูกดึงตามความต้องการของลูกค้า
5. ความสมบูรณ์แบบ เป็นความสามารถในการทำให้ถูกต้องตั้งแต่แรกเริ่ม โดยการปรับปรุงอย่างต่อเนื่อง
ลีนจะประสบความสำเร็จ ต้องประกอบไปด้วยองค์ประกอบเหล่านี้
1. ความเข้มแข็งของภาวะผู้นำ ทั้งในการแสดงและสื่อวิสัยทัศน์ การอำนวยการและการกำหนดรูปแบบ การสร้างมาตรฐานองค์กร การให้คำแนะนำทีมไปสู่การเปลี่ยนแปลง สร้างความเชื่อมั่น เพื่อไปสู่สิ่งที่ดีกว่า
2. วัฒนธรรมของทีม ในการใช้รูปแบบโครงการ ทีมจะผลักดันส่วนร่วม สมดุลระหว่างสมาชิกในเรื่องของความรู้ โดยใช้พนักงานที่มีประสบการณ์มาช่วยพัฒนาให้เกิดความต่อเนื่องของทีม
3. ระบบการสื่อสารและระบบการทำงาน ที่ช่วยในการตัดสินใจในจุดเดียว โดยใช้ทรัพยากรน้อยที่สุด มีการสื่อสารแบบเป็นทางการและไม่เป็นทางการ มีการแลกเปลี่ยนความรู้กัน
เพื่อตอบรับกับการทำงานของเราและลูกค้าการดำเนินการลีนจะเริ่มอย่างไร
ต้องมีการสร้างทีมงานและผู้บริหารมีหน้าที่ดูแลระบบลีน คือ ลีนมาสเตอร์ จะมีการดำเนินการดังนี้ ควรต้องทำความเข้าใจกับลีนและกรอบการวัดของมัน เรียนรู้ผ่านการศึกษาธุรกิจ ผู้นำองค์กรเป็นผู้กำหนดกลไกการมุ่งสู่ลีนองค์กร มีการจัดทำแผนทั้งระยะสั้นและยาว กำหนดตัววัดฐานก่อนเริ่มทำลีน กำหนดแผนโครงการและผู้รับบทบาทลีนมาสเตอร์ เพื่อรับหน้าที่หลักในการดูแลระบบลีน หลังจากนั้นมีการตั้งลีนแมนเนเจอร์และทีมงาน โดยการเรียนไปพร้อมๆกัน โดนลีนมาสเตอร์เป็นผู้กำหนดพื้นที่ปฏิบัติการ
ดังนั้น การดำเนินการเพื่อการมุ่งสู่การผลิตแบบลีน จำเป็นต้องมีการกำหนดแผนกลยุทธ์ โดยผู้บริหารระดับสูง และมีการจัดทำแผนการเปลี่ยนแปลงกระบวนการที่ชัดเจน พร้อมกับการใช้วิธีการเรียนไปพร้อมกับการลงมือปฏิบัติ จึงจะสามารถประสบความสำเร็จได้
Create Date : 28 ตุลาคม 2551 |
Last Update : 9 กรกฎาคม 2552 8:49:23 น. |
|
0 comments
|
Counter : 1278 Pageviews. |
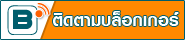 |
|
|
| |
|
|